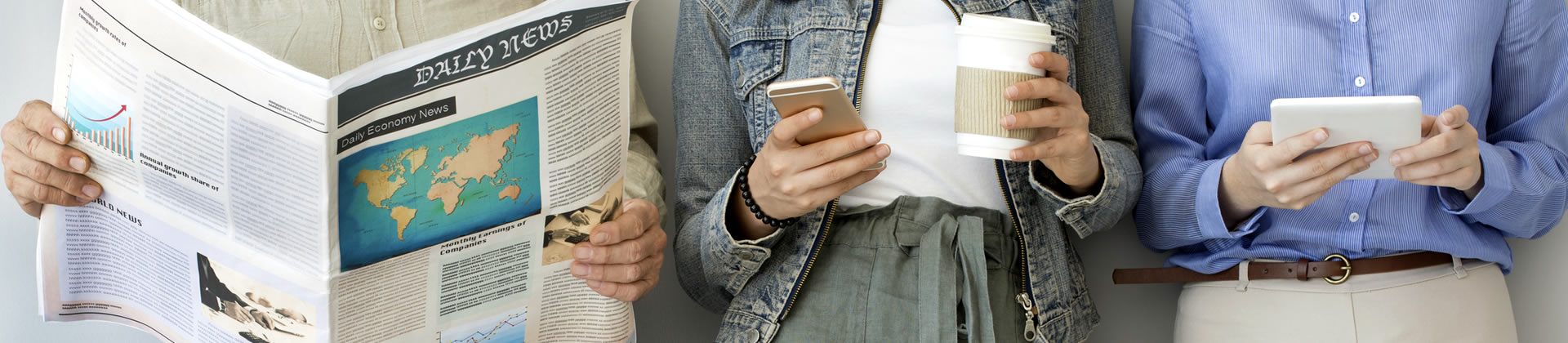
Manufacturing Software – The Ultimate Guide to Great Support
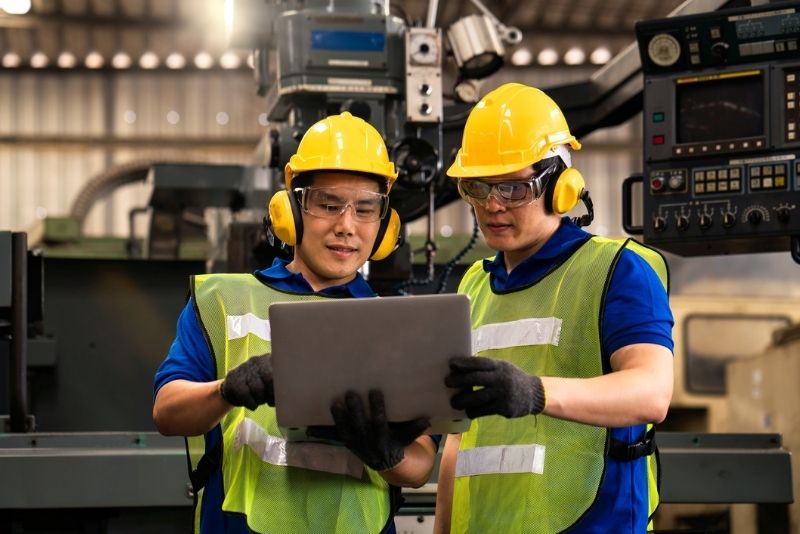
Manufacturing Software – The Ultimate Guide to Great Support
At P1 Technology, we support many clients in the manufacturing and food services sector.
We’re big supporters of keeping things local, and it’s our privilege to help manufacturers from industries such as packaging, food manufacture and processing, sheet metal, duct and air extraction, custom metal works, 4WD and race car accessories and modifications, pet and animal accessories and clothing/uniform design, to deliver their products to customers across the world.
Whatever manufacturing is your specialty, the one thing you have in common with every other manufacturer, is that you need specialised software to run your business efficiently.
What’s so special about manufacturing software?
It’s often niche, and can even be exclusive not just to manufacturing, but to a specific industry.
This means that it’s not something your average IT provider or technician will have experience in. So, when something goes wrong, or you’ve got a question about the piece of software or the systems and machinery it controls, your IT person will likely ask you who supports the system.
Who do you contact for specialised support?
Most IT support experts have experience in a wide range of software that’s common to business.
But, when it’s reasonably unusual or industry specific, there’s a good change they haven’t seen it before and can only troubleshoot to a point before they’ll need to reach out to someone who has specialised advice.
This is where your IT partner will need access to a software specific support contact.
Not knowing the answer can be costly.
It’s a common problem to find business owners who don’t have this information handy, or have been taking shortcuts with their support contracts.
It’s true that specialist software can incur higher costs for support. But when a piece of software required more than the usual range of knowledge, you’ll find yourself in a bind to simply rely on your IT person (or internal staff) to just figure it out.
Often the savings you make in specialist support costs end up being significantly outweighed by downtime, lost productivity or and excessive investment in unqualified people trying to fix a problem they don’t have enough experience in.
What’s the answer?
Here’s my Ultimate Guide to getting great support for your manufacturing software.
1. Keep a detailed contact record
Keep a detailed record of who to call for support and how to reach them for every machine and software system in your manufacturing business.
2. Have a Support Contract in place
Pay for specialised support and make sure that you keep your support contracts current so you can access ongoing, time-sensitive support when you need it.
3. Remember that support contracts keep your systems current
When you’ve got a support contract in place, you’ll get access to updated systems along the way. There’s no point in saving $10,000 over five years, for it to cost you $20,000 and a heart attack to resolve the problem when it does arise.
Be proactive, not reactive.
4. Document software and systems information
Make sure you keep all the details about how your software and systems work, documented. Don’t rely on it all being in someone’s head.
It might be tempting to let support or warranty contracts lapse…
But ask yourself this.
What happens if a piece of machinery doesn’t work for a day, or a week?
What would the cost of this be to your business? In sales, in staff overheads, in time, in stress?
Invest in the right support for your manufacturing software and systems. Pass on the costs to your clients (remembering the quality of product and service they will receive because you’ve got your bases covered and your risks mitigated).
And rest easy knowing that you’ve got great support that’s only a phone call away.
« Back to News